Boost Welding Requirements with Specialist Inspection Service
Boost Welding Requirements with Specialist Inspection Service
Blog Article
Browsing the World of Welding Providers: A Comprehensive Guide to Types and Benefits
In the world of commercial applications and construction projects, the relevance of welding solutions can not be overemphasized. Welding is a basic process that binds products with each other, ensuring architectural integrity and durability. Nonetheless, the world of welding solutions is huge and differed, supplying various kinds of methods customized to particular demands and demands. As we begin on this thorough guide to the kinds and benefits of welding services, we will certainly delve right into the complexities of numerous welding procedures, discover the benefits of MIG and TIG welding, and clarified the specialized methods that accommodate distinct projects. Stay tuned to uncover how browsing the varied landscape of welding services can raise the top quality and performance of your following endeavor.

Different Types of Welding Processes
Various strategies are used in welding procedures to sign up with products with each other effectively and safely. One common welding technique is Secured Metal Arc Welding (SMAW), also known as stick welding.
Another commonly used strategy is Gas Steel Arc Welding (GMAW), or MIG welding. In this procedure, a cable electrode is fed through a welding weapon, which additionally launches a protecting gas to secure the weld from contaminants in the air. GMAW is understood for its rate and ease of usage, making it ideal for manufacturing and automotive industries.
Furthermore, Gas Tungsten Arc Welding (GTAW), or TIG welding, is favored for its precision and clean welds. If required, TIG welding uses a non-consumable tungsten electrode and a separate filler product. This technique is typically utilized in aerospace, automobile, and creative applications because of its ability to develop high-grade welds
Benefits of MIG Welding
MIG welding, also referred to as Gas Steel Arc Welding (GMAW), provides distinct benefits over other welding procedures, making it a preferred choice in production and automobile markets. Among the key benefits of MIG welding is its flexibility. This procedure can be made use of on a wide variety of steels and densities, including light weight aluminum, stainless steel, and mild steel. Furthermore, MIG welding is recognized for its high welding speeds, resulting in increased performance. The process is reasonably simple to execute and learn, making it ideal for both newbies and skilled welders.
Moreover, MIG welding generates clean welds with marginal spatter, decreasing the demand for substantial post-weld cleanup. The usage of a protecting gas in MIG welding protects the weld pool from pollutants in the environment, leading to high-grade, strong welds. One more advantage of MIG welding is its ability to be automated, permitting accurate and consistent welds in automation setups. Generally, the advantages of MIG welding make it a prominent selection for various applications where performance, quality, and ease of use are important.
Advantages of TIG Welding
Tungsten Inert Gas (TIG) welding, likewise referred to as Gas Tungsten Arc Welding (GTAW), sticks out in the welding market for its specific control and high-quality welds. One of the key benefits of TIG welding is its ability to generate clean and aesthetically pleasing welds without the requirement for filler material. This causes welds that call for marginal post-weld cleaning and sprucing up, making TIG welding perfect for applications where appearance is essential.
Furthermore, TIG welding is appropriate for Going Here welding thin products anonymous as a result of its reduced heat input and precise control over the welding arc. This makes it a favored choice for markets such as aerospace, auto, and electronics, where welding slim sections without distortion is crucial.

Discovering Arc Welding Techniques
When diving right into the world of welding methods, one comes across a diverse selection of arc welding techniques that play a critical duty in numerous commercial applications. One of the most typical arc welding methods is Secured Steel Arc Welding (SMAW), additionally known as stick welding, which is preferred for its convenience and simpleness.
An additional prevalent arc welding method is Gas Metal Arc Welding (GMAW), frequently referred to as MIG (Metal Inert Gas) welding. In general, arc welding methods offer an array of options to provide to varied welding needs across different industries.
Recognizing Specialty Welding Solutions
Specialized welding solutions play an important role in satisfying the special demands of intricate industrial tasks and precision applications. These services go beyond conventional welding methods to deal with specific obstacles that standard methods might not efficiently resolve. Specialized welding includes a large range of innovative procedures tailored to meet the requirements of specialized markets such as aerospace, auto, and production.
One trick aspect of specialty welding services is the capacity to function with exotic materials that require specific expertise and devices. This includes welding procedures for products official site like titanium, magnesium, and different high-strength alloys, which demand a high degree of ability and accuracy to ensure ideal outcomes.
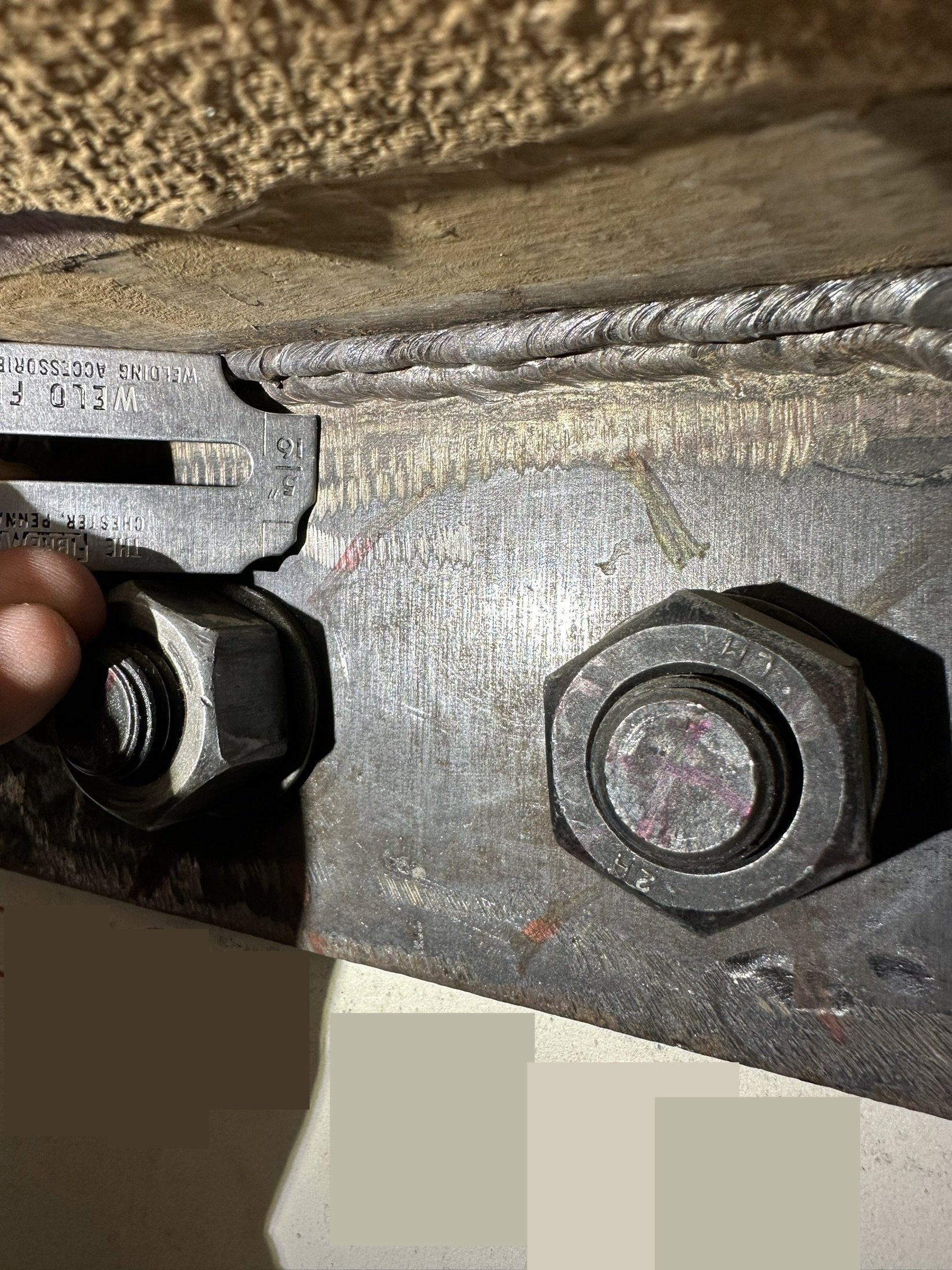
Fundamentally, specialty welding solutions are vital for industries that demand the highest standards of high quality, toughness, and precision in their welding projects. By leveraging specialized strategies and experience, these solutions enable services to tackle complicated difficulties and attain premium cause their operations.
Verdict
To conclude, understanding the different kinds of welding procedures and their advantages is crucial for navigating the world of welding solutions. MIG welding supplies advantages such as high performance and simplicity of usage, while TIG welding provides benefits like exact control and tidy welds. Checking out arc welding strategies and specialty welding solutions can better broaden the alternatives and capacities readily available for various welding tasks. By familiarizing oneself with these different options, individuals can make enlightened decisions when selecting welding services.
As we begin on this extensive overview to the types and advantages of welding solutions, we will dive into the intricacies of different welding processes, reveal the benefits of MIG and TIG welding, and lost light on the specialized techniques that provide to special projects. One usual welding method is Protected Steel Arc Welding (SMAW), additionally understood as stick welding.MIG welding, additionally understood as Gas Metal Arc Welding (GMAW), offers unique advantages over other welding procedures, making it a recommended choice in manufacturing and vehicle industries.Tungsten Inert Gas (TIG) welding, likewise recognized as Gas Tungsten Arc Welding (GTAW), stands out in the welding industry for its specific control and premium welds.One more prevalent arc welding technique is Gas Steel Arc Welding (GMAW), frequently referred to as MIG (Steel Inert Gas) welding.
Report this page